TERAO is part of the Hub of Low Carbon Prescribers. We have previously shared summaries of the thematic briefs “Facades” and “Bio-based materials“.
In 2023, the Hub continued its approach to supporting prescription through renovation case studies, to understand and achieve the optimal cost and carbon of renovation on existing projects. This work will be the subject of several briefs throughout its progress.
Here we present the key messages from Brief n°1 – Low-carbon renovation “Measure to act, how to measure effectively and pragmatically the carbon footprint of a renovation?”.
KEY MESSAGE N°1: A new construction/renovation equation is emerging
In France, the National Low Carbon Strategy (SNBC) aims for the building sector to achieve complete decarbonization of the operating phases by 2050.
In France, the building sector is the second largest emitter of greenhouse gases. In 2019, it was responsible for 25% of the country’s carbon footprint. These emissions are divided between emissions related to the operation of buildings (Scope 1 + Scope 2 = 67% of the total), and those related to components (Scope 3 = 33% remaining).
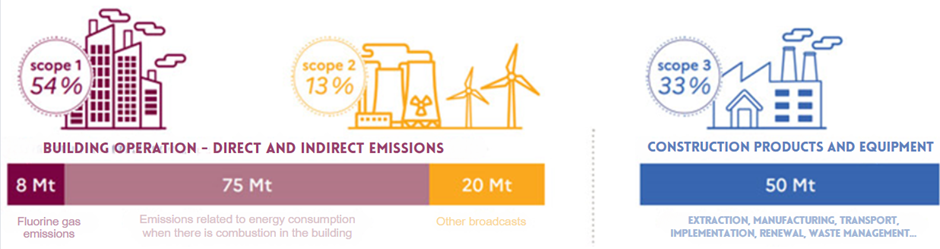
© Building Lifecycle Decarbonization Roadmap
To meet the SNBC objective, it is necessary to build new, low-carbon and energy-efficient buildings, but also and above all to drastically improve the energy performance of the existing fleet, while limiting the emissions related to the materials and equipment used.
KEY MESSAGE N°2: A carbon budget for materials dedicated to renovation is essential
To allow medium-term visibility of the carbon reduction trajectories to be respected, the SNBC sets national GHG emission ceilings not to be exceeded per 5-year period (carbon budgets) consistent with the trajectory aiming at carbon neutrality and indicative annual carbon budgets.
Today, the carbon budget allocated to the building sector for the operation of these and building materials does not distinguish between the new and renovation sectors.
The new construction sector is governed by efficient and progressive Environmental Regulations.
Today, the regulatory aspects related to renovation only concern energy: Existing RT, Tertiary Decree, Energy Performance Diagnosis.
Voluntary labels exist (BBC Effinergie Rénovation – version 2024 to come and BBCA Rénovation) and accounting methods are being developed (NZC Renovation Programme, Quartier Energie Carbone Method, Renovation Method of the Low Carbon label).
As it stands, while there were well over 700,000 renovation actions in 2022, only 66,000 homes were renovated overall, which is well below the figures estimated by the SNBC (or by the summary of ADEME, NegaWatt, The Shift Project, Pouget Consultants and Carbone 4 (2022)) scenarios to achieve the objective of carbon neutrality by 2050.
The Hub proposes the definition of a carbon budget for materials specific to renovation:
➡ A carbon budget specific to materials within the sectors of the economy;
➡ With the definition of two separate new/renovation allocations of this budget for the building sector.
Compliance with this budget will be conditioned by two fundamental points:
➡ The ability of stakeholders to “count carbon in the life cycle” of their renovation operations;
➡ The objectification of renovation operations through criteria to be respected to stay within the limits of these budgets, for example, quantified thresholds.
KEY MESSAGE N°3: Two distinct battles: decarbonizing energy, and preserving material resources
The renovation types are usually distinguished according to the number and nature of the affected lots: from “light” to “heavy” renovation. A different interpretation is necessary in our case.
If we want to allocate a carbon budget linked to materials for energy renovation, it seems more relevant to segment the renovation materials budget into two: the part related to energy performance and the part related to quality of use.
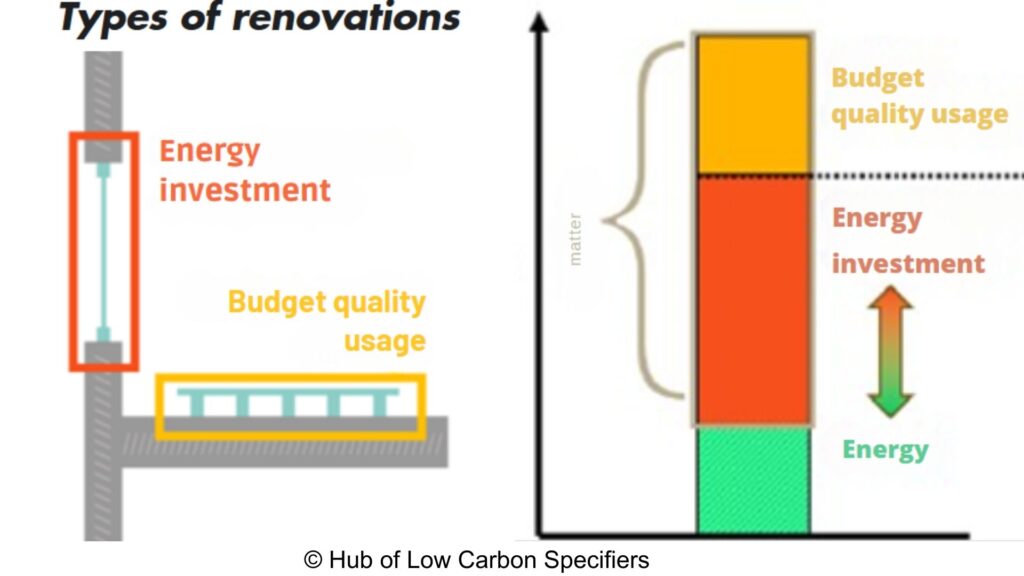
Energy investment
- This investment involves retrofitting the building envelope and/or equipment that impacts energy performance.
- There is a balance between the carbon impact of these materials and the reduction of the carbon impact of the energy in operation.
- This balance point makes it possible to respect the objective of improving the existing.
Quality budget used
- This budget involves replacing obsolete materials (technically, architecturally, aesthetically, or simply out of habit) that do not affect energy performance.
- The goal is to reduce the carbon impact of the material (as in RE2020 for new construction).
- It does not improve carbon efficiency in operation.
Carbon payback time (CRT)
One measure of the carbon footprint of energy retrofits is the Carbon Payback Time (CRT):

KEY MESSAGE N°4: Eliminate fossil fuels as quickly as possible
During the renovation, the primary goal is often to improve comfort and/or reduce energy consumption, while changing the energy system can take a back seat. However, from a carbon perspective, the number one lever for decarbonizing a building is to move away from fossil fuels, with the potential to increase carbon footprint very significantly, up to 800 kgCO2e/m² (divided by 10) in the case of one of the Hub’s case studies.
Getting out of fossil fuels…
If we set a carbon payback time objective, a major renovation will necessarily involve the question of phasing out fossil fuels to be relevant.
… as quickly as possible
The later a renovation is completed, the more operating emissions are accumulated that could have been avoided by renovating earlier.
Regardless of the type or purpose of the renovation, the building must address comfort, consumption and decarbonization. These three pillars must be taken into account during operation, ideally at the time of construction, possibly in a medium-term plan. |
KEY MESSAGE N°5: The conservation of what already exists is a fundamental issue and requires a paradigm shift
Unlike a new construction project, which is designed to meet a program, a renovation project is carried out in such a way that the program is adapted to the existing building. Indeed, it is necessary to address many parameters that characterize the existing building (surface, orientation, usage, condition of the existing building, etc.).
Renovation requires specific work and a collective transformation of methods to be relevant and effective. From a constraint, the existing must become a treasure trove of available resources, in other words, a local material bank. The carbon weight of new material depends almost entirely on what can be retained and the carbon weight of the quality used.
Conserving as much material as possible is the first and greatest lever to decarbonize renovation materials. Once the existing has been preserved as much as possible, reuse must be the number two action.
A prerequisite for maintaining what is in place is the implementation of a resource/reuse diagnosis, including a more advanced version of the prescribed MDP diagnosis. It must be able to demonstrate conservation potential, i.e. the proportion of materials that can be preserved.
In addition to carrying out the various diagnoses, the ability to reuse during a renovation project also depends on three factors:
✔ Insurability of reused equipment
✔ Applicable taxation
✔ Prioritize Project Owners to reuse as early as possible in the project
KEY MESSAGE N°6: Optimize the carbon weight of materials
Unlike new construction under RE2020, where the carbon weight of materials is divided into three equal parts (structural work, finished work and technical lots), the projects studied in renovation have a different distribution. Indeed, the technical packages represent 60% of the carbon weight of the material being renovated, according to the first case studies conducted by the Hub.
The HVAC package is the first item in the total carbon weight of materials: it represents between 25% and 40% of the total.
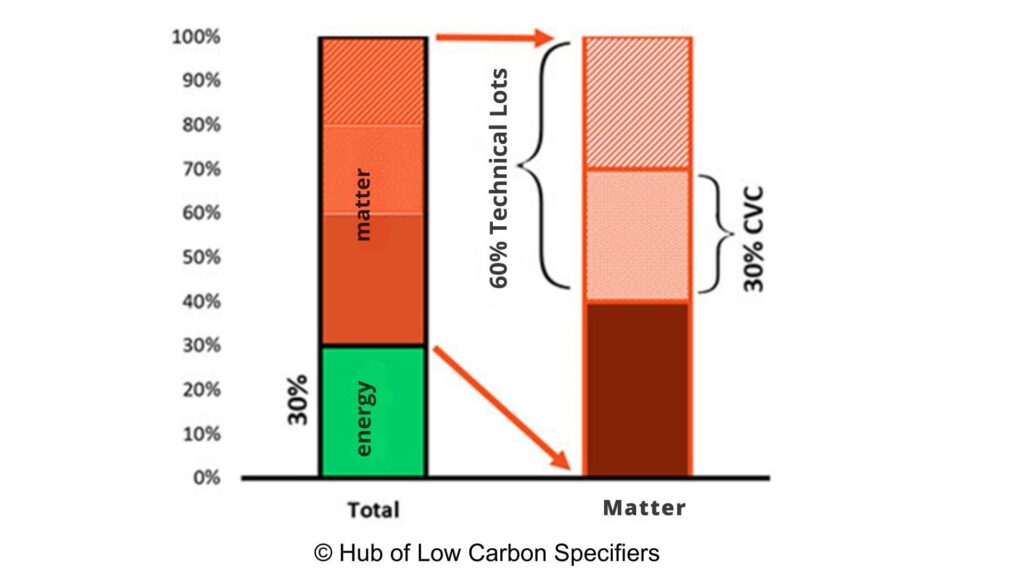
The optimization of these batches contributes significantly to the reduction of the carbon weight of Materials (up to -50% according to the Hub’s case studies) as well as that of the Energy contributor (up to -90%). However, a detailed LCA is required to determine the details and identify relevant optimizations.
On this topic, the Hub published a Brief on technical lots at the end of 2022 providing guidance, supported by specific case studies, on undervalued fix-rate technical lots where a detailed approach is beneficial for LCA.
The main lever is saving and reuse (if possible) for technical lots, the second lever is the deployment of less carbon-intensive equipment through detailed LCA calculation of targeted lots.
Contrary to what one might imagine, the structural work package is rarely zero in renovation and can account for a significant portion (up to 15%) of the total carbon weight of the material, as foundation reinforcement or structural reworking is often required.
NOTE: contrary to what one might imagine, the structural work package is rarely zero in renovation and can account for a significant portion (up to 15%) of the total carbon weight of the material, as foundation reinforcement or structural reworking is often required. |
KEY MESSAGE N°7: Rehabilitation is an approach and specific constraints, integrated from the design stage
To conclude these messages, it is clear that the approach to designing a low-carbon retrofit is very different to a new project, because not all existing buildings are equal when it comes to decarbonization.
First of all, the heritage is particular. Because of its specific architecture, and specific to a particular use, the heritage requires more substantial work than a “classic” thermal renovation of a house; and obligations can be distinguished. For example, the future planning of a heritage building, which often involves a change of use, must be calculated for the building rather than a hypothetical on the ground.
Furthermore, all existing buildings, in addition to the huge resources they represent (see message n°5), require more extensive and intensive work than a new project. Rehabilitation imposes specific constraints to be anticipated as much as possible.
Some examples |
The ceiling height, which is sometimes too high, can make it difficult to optimise compactness. |
It can be too weak and make it impossible to pass through technical ducts. |
Structural reinforcement, if necessary, can quickly increase the carbon footprint and require specific optimization. |
The program, especially summer comfort, can be very energy-consuming. |
The carbon weight of the material Quality of use can easily reach orders of magnitude comparable to new. |
NOTE: insulation is always a good carbon investment according to the feedback from all Hub members. Indeed, reducing heating needs contributes significantly to reducing the carbon impact of energy in operation, from 40% to 90%. Using bio-based insulation makes this carbon investment even more interesting. |
We recommend the application of the following reasoning for the decarbonization of any renovation project
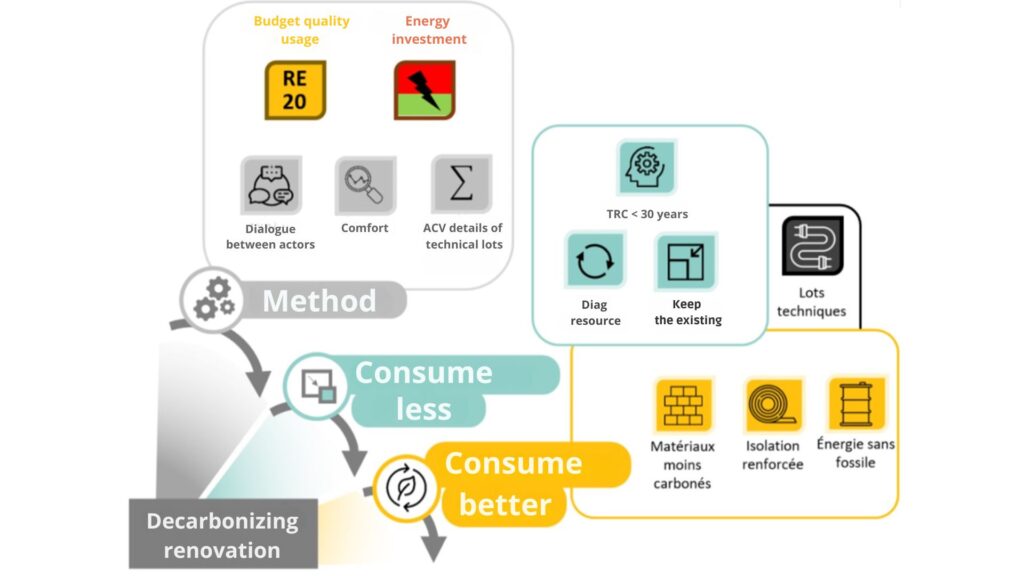
© Hub of Low Carbon Specifiers
Original article on TERAO.fr website: CARBON-FREE RENOVATION: THE RENOVATION BRIEF (terao.fr)
Leave A Comment