Factories consume a large amount of energy for various operations, such as heating, cooling, lighting, machinery, etc. A significant portion of this energy is wasted as heat, which not only increases the operational costs, but also contributes to greenhouse gas emissions and environmental degradation. Thermal optimization can help factories to reduce their energy consumption and carbon footprint, while also enhancing their productivity and profitability.

Energy consumption within semiconductor manufacturing facilities
Thermal optimization of factories is the process of improving the efficiency and performance of industrial processes by reducing the heat losses and maximizing the heat recovery. It is important because it can reduce the environmental impact of factories, lower the operational costs, improve the product quality, and enhance the safety and comfort of workers.
Why is thermal optimization of factories important?
First, it can help you save money on energy bills. According to the U.S. Department of Energy, industrial facilities account for about 32% of total U.S. energy consumption and 28% of U.S. greenhouse gas emissions. By optimizing the thermal performance of your factory, you can reduce your energy demand and improve your energy efficiency. This can translate into significant cost savings over time.
Second, thermal optimization can help you increase productivity and quality. By maintaining the optimal thermal conditions for your factory processes and equipment, you can improve their performance and reliability. This can result in higher output, lower downtime, fewer defects, and better customer satisfaction.
Third, thermal optimization can help you enhance safety and comfort. By regulating the temperature and humidity levels in your factory spaces, you can prevent overheating, freezing, condensation, corrosion, mold growth, and other issues that can affect the health and well-being of your workers and visitors. This can reduce the risk of accidents, injuries, illnesses, and lawsuits.
Fourth, thermal optimization can help you lower environmental impact. By reducing your energy consumption and emissions, you can minimize your carbon footprint and contribute to the global efforts to combat climate change. This can also improve your reputation and compliance with environmental regulations and standards.
Thermal optimization involves two main steps: heat loss reduction and heat recovery.
Heat loss reduction refers to preventing or minimizing the unwanted transfer of heat from the process to the surroundings. This can be achieved by:
– Improving the insulation of pipes, equipment and buildings
– Reducing air infiltration and ventilation losses
– Eliminating steam leaks and condensate losses
– Optimizing process temperatures and pressures
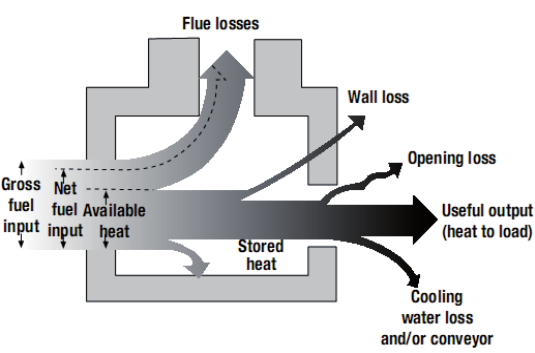
Heat losses in industrial heating processes
Heat recovery refers to capturing and reusing the excess or waste heat from one process to another process that requires heat. This can be achieved by:
– Installing heat exchangers, heat pumps or cogeneration systems
– Integrating processes with complementary heating and cooling needs
– Utilizing waste heat for space heating, water heating or power generation
– Recovering heat from flue gases, exhaust air or cooling water
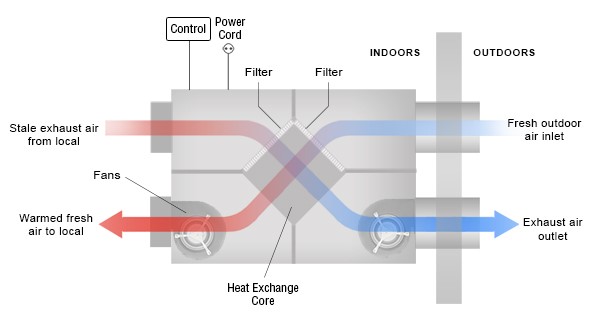
Heat recovery: Overview
The benefits of thermal optimization are manifold. It can improve the productivity and quality of the products, as well as worker safety and comfort. It can also reduce the greenhouse gas emissions and the dependence on fossil fuels, as well as the maintenance and operating costs. According to some studies, thermal optimization can save up to 20% of the energy consumption and up to 30% of the carbon dioxide emissions of a factory.
How to Achieve Thermal Optimization of Factories
Thermal optimization can be achieved in different types of factories by applying various strategies and technologies, such as:
– Conducting a thermal audit. A thermal audit is a systematic assessment of the sources and sinks of heat in a factory, as well as the potential for heat recovery and reuse. A thermal audit can help identify the areas where heat loss is occurring, quantify the amount and quality of heat that is available, and evaluate the feasibility and cost-effectiveness of different solutions.
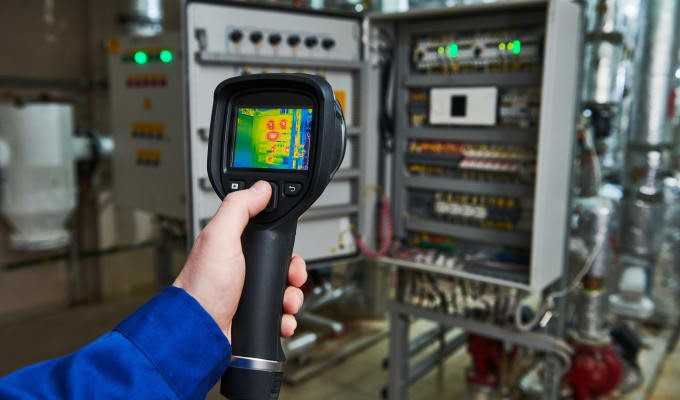
– Implementing heat recovery systems. Heat recovery systems are devices that capture the waste heat from one process and use it for another purpose, such as heating, cooling or power generation. Heat recovery systems can be classified into two types: passive and active. Passive systems rely on natural phenomena, such as conduction, convection or radiation, to transfer heat from one medium to another. Active systems use mechanical devices, such as pumps, fans or compressors, to move heat from one medium to another. Examples of heat recovery systems include heat exchangers, heat pipes, thermoelectric generators, organic Rankine cycles and absorption chillers.
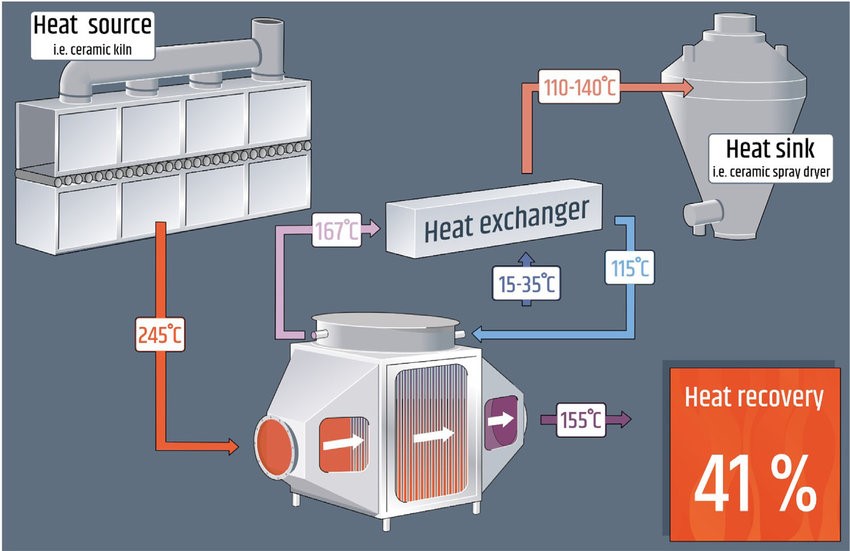
Heat recovery system
– Optimizing heat distribution systems. Heat distribution systems are networks of pipes, ducts or wires that transport heat from one location to another within a factory. Heat distribution systems can be optimized by using proper insulation materials, minimizing leaks or losses, adjusting flow rates or pressures, and balancing supply and demand.
– Adopting smart control systems. Smart control systems are software or hardware tools that monitor and regulate the temperature, humidity and airflow in a factory. Smart control systems can use sensors, actuators, algorithms or artificial intelligence to optimize the performance of heating, ventilation and air conditioning (HVAC) systems, as well as other equipment or processes that generate or consume heat.
– Implementing best practices and standards. Best practices and standards are guidelines or recommendations that provide general or specific advice on how to achieve thermal optimization in a factory. Best practices and standards can be developed by industry associations, government agencies, research institutions or other stakeholders. Examples of best practices and standards include ISO 50001 (Energy management systems), ISO 14001 (Environmental management systems) and LEED (Leadership in Energy and Environmental Design).
Thermal optimization of factories is a topic that deserves your attention and action. It can help you achieve your environmental and economic goals, while enhancing your competitive edge and reputation. We hope that this blog post has given you some useful insights and tips on how to optimize your thermal performance. If you want to learn more or get professional assistance, please contact our Business Development Director, Mr. Gaspard at glemoinescelles@teraoasia.com or visit our website.
探索更多。
– [Expertise] Energy modelling: a powerful tool for sustainable buildings
– [Case study] Fordia – Energy efficiency and energy savings opportunities in industry
– [Expertise] Thermal comfort improvement for factories – the right approach
留下评论